My Emco V13 lathe came with a four way toolpost. I'd rather do dishes than use shims, so that had to go. I have a 200 series KDK post with around 8 holders, so that'd be the obvious way to go. Unfortunately the press fit screw used to hold the post in the emco didn't fit the KDK --- too small at top, too large at bottom. I couldn't modify the KDK either --- it's hard enough that it ate some carbide endmills I tried to use to cut it and probably woke the neighborhood. And there's no dovetail on the emco.
So we need to make a new bushing to press fit into the compound rest. It was thanksgiving eve, so it was a perfect project. (I don't have a TV.)
Here's the emco's compound rest w/ the tool post screw sticking out:
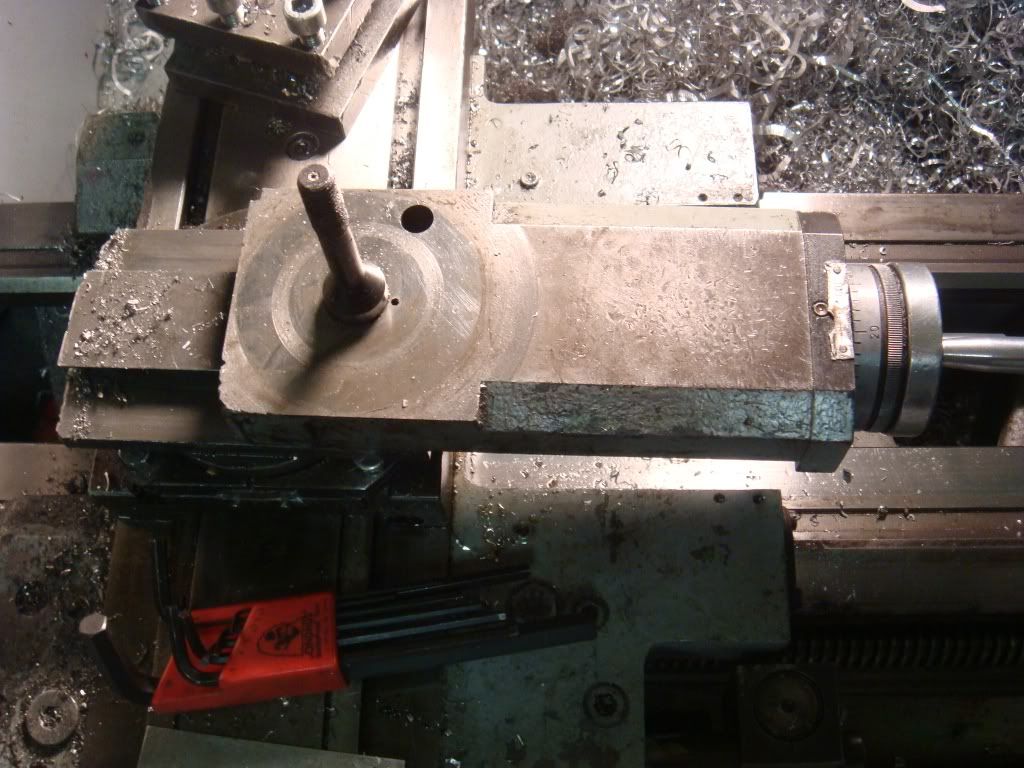
To get at it we have to remove the rest and the handle. I'd done them in that order previously, so did it in the opposite this time. It's easy enough: allen screws out:
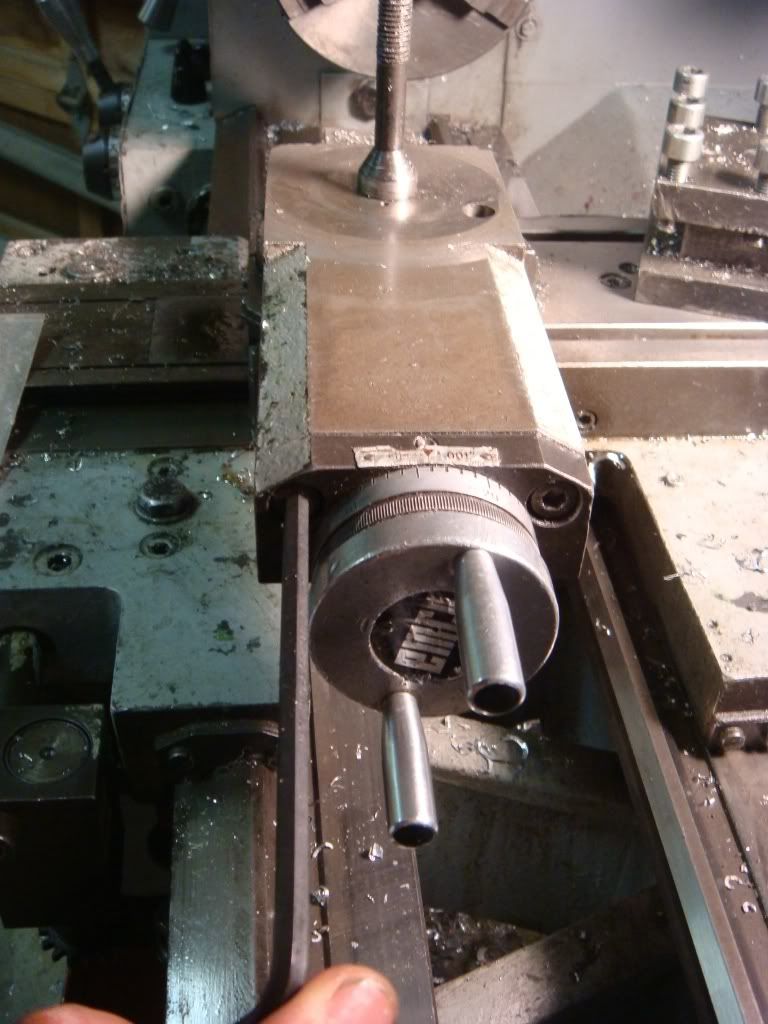
Then the whole end comes off (after you've moved the rest back):
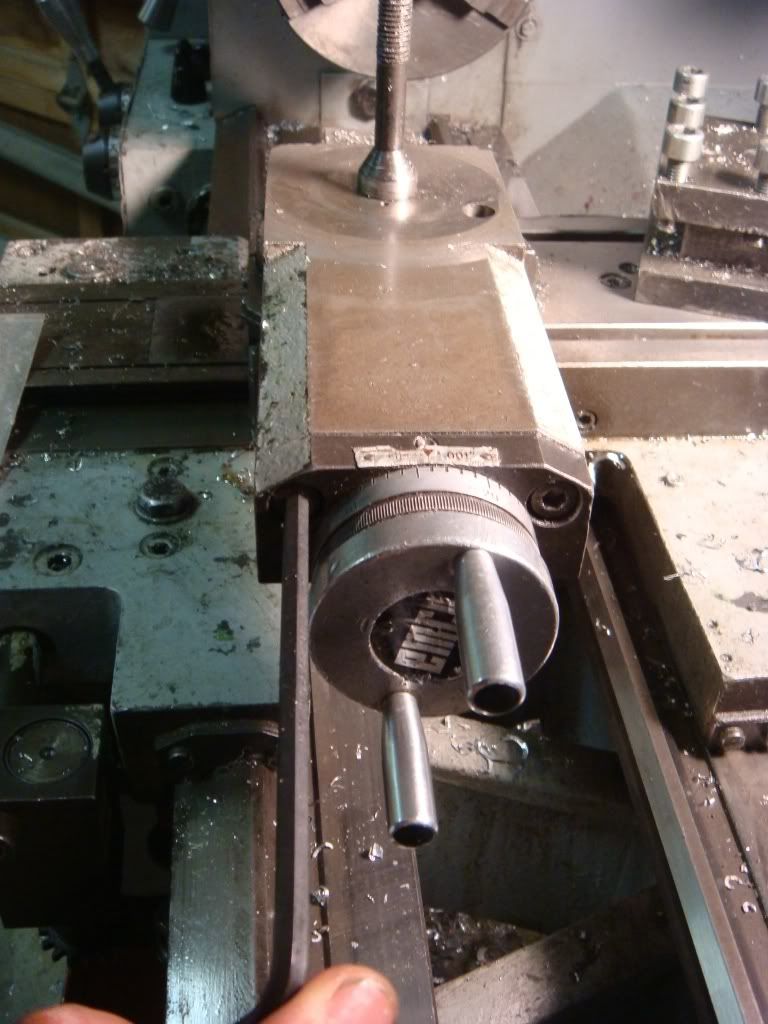
The gib and also a narrow sheet of metal (added later?):
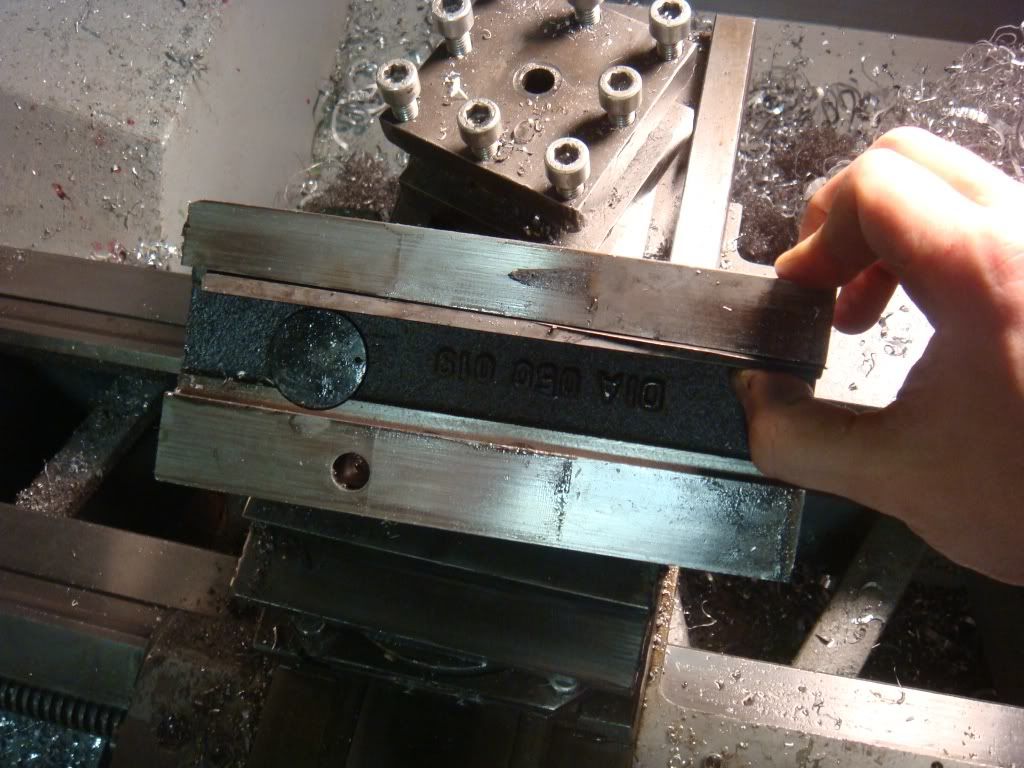
You can't see it but there is a notch that has to lock into the gib adjusting screw at the left side.
Here's the press fit we have to knock out. There's also a pin in there for alignment: I think to ensure you orientate the screw in such a way that you can't run the handle into the chuck at the tightest position:
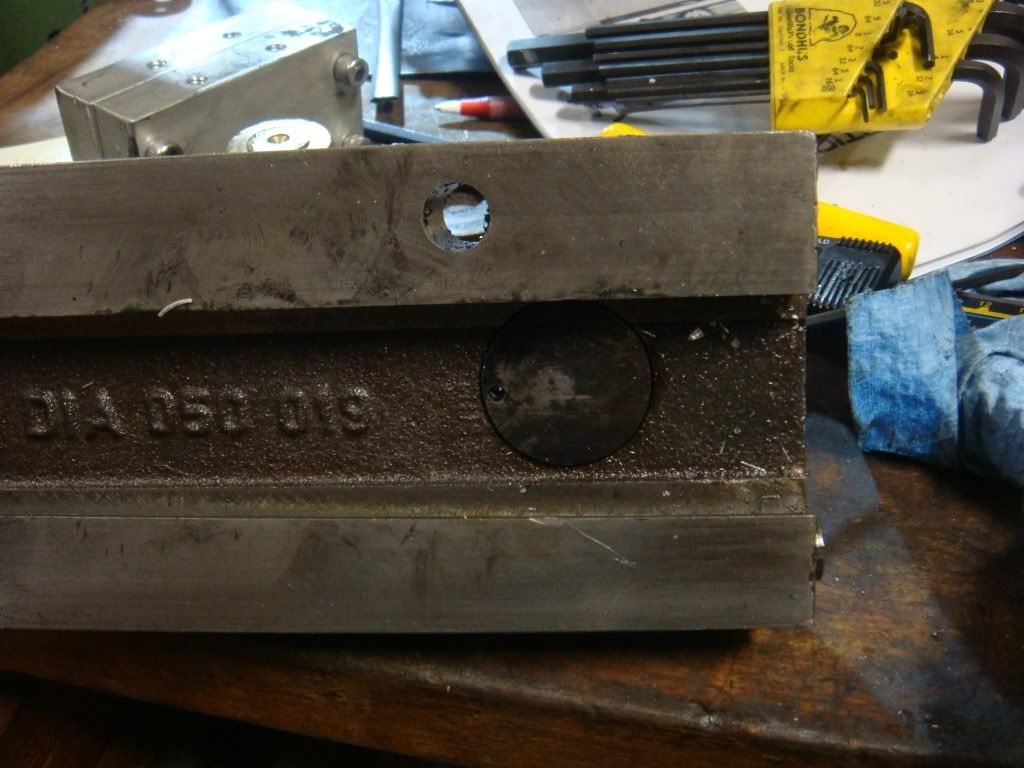
We're going to screw the KDK down w/ a 3/4" bolt. So will replace the screw with a bushing tapped to the right threads. Unfortunately the only stock I had large enough was some SS, so figured it was going to be a fairly tedious adventure.
First problem is that I didn't have a tap wrench big enough to hold the 3/4" tap needed to cut threads into the bushing. So, since it was late and the stores would be closed the next day in any case, went ahead and jury rigged a ghetto stap setup using a live center to hold the tap in the right location, holding the to-be bushing in a 3-jaw, and rotating the chuck by hand to cut the tap into it.
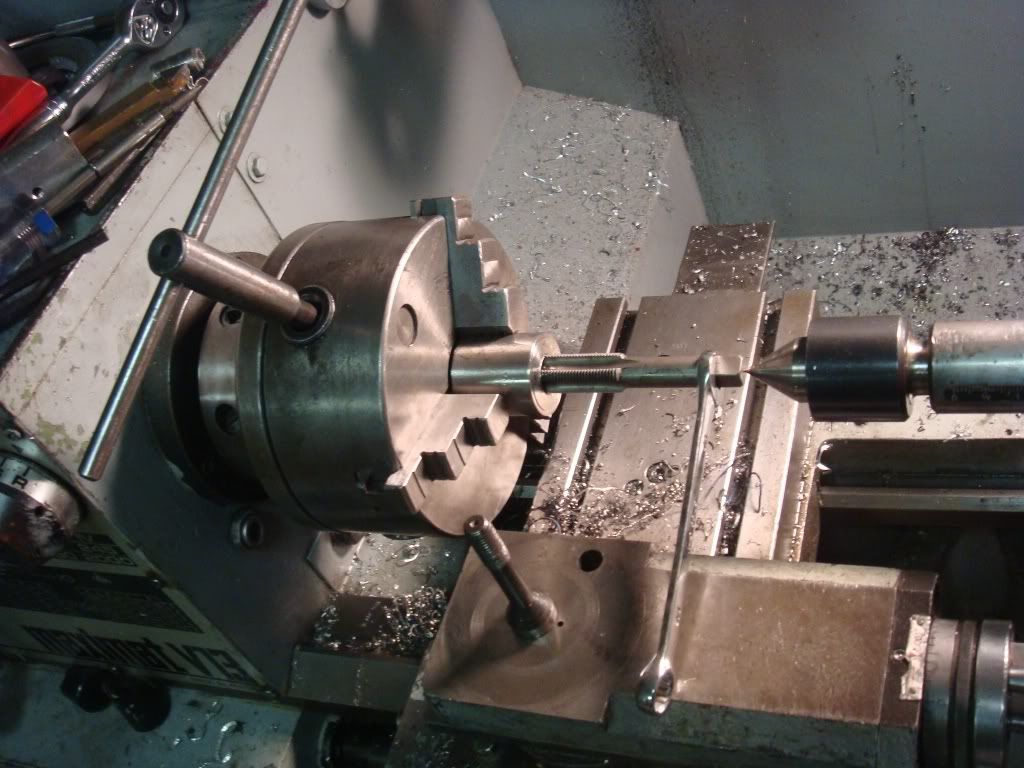
This worked surprisingly well and we wind up with a SS cylinder that we can screw our bolt into:
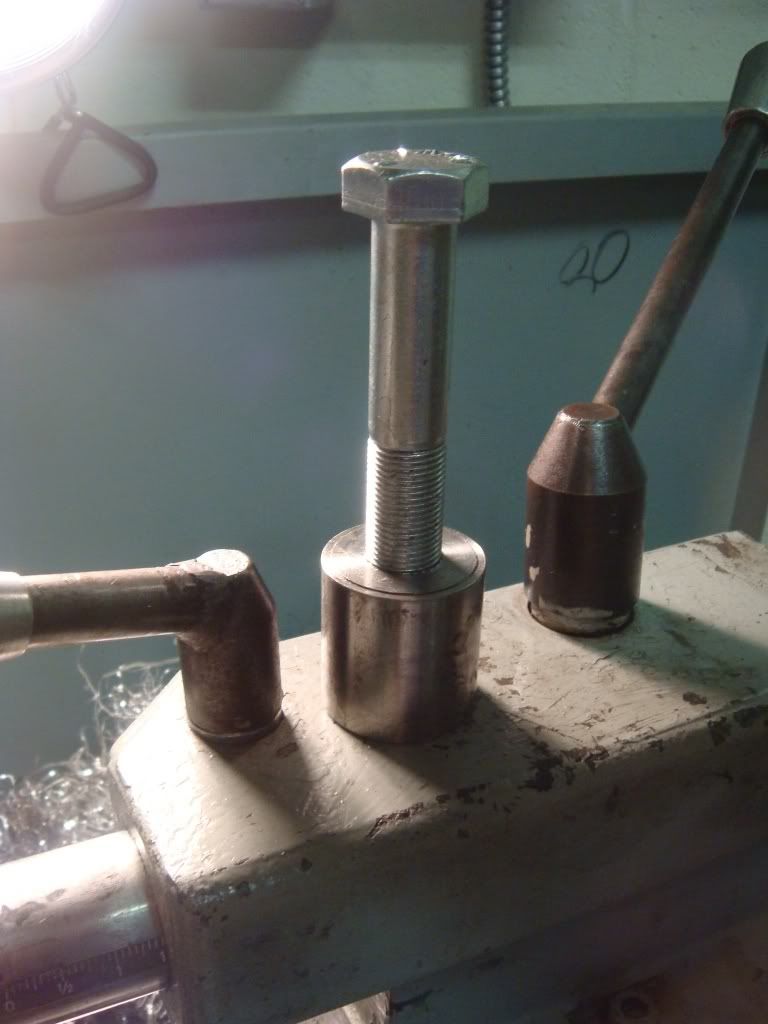
We then cut the busing down so that it fits in the compound rest:
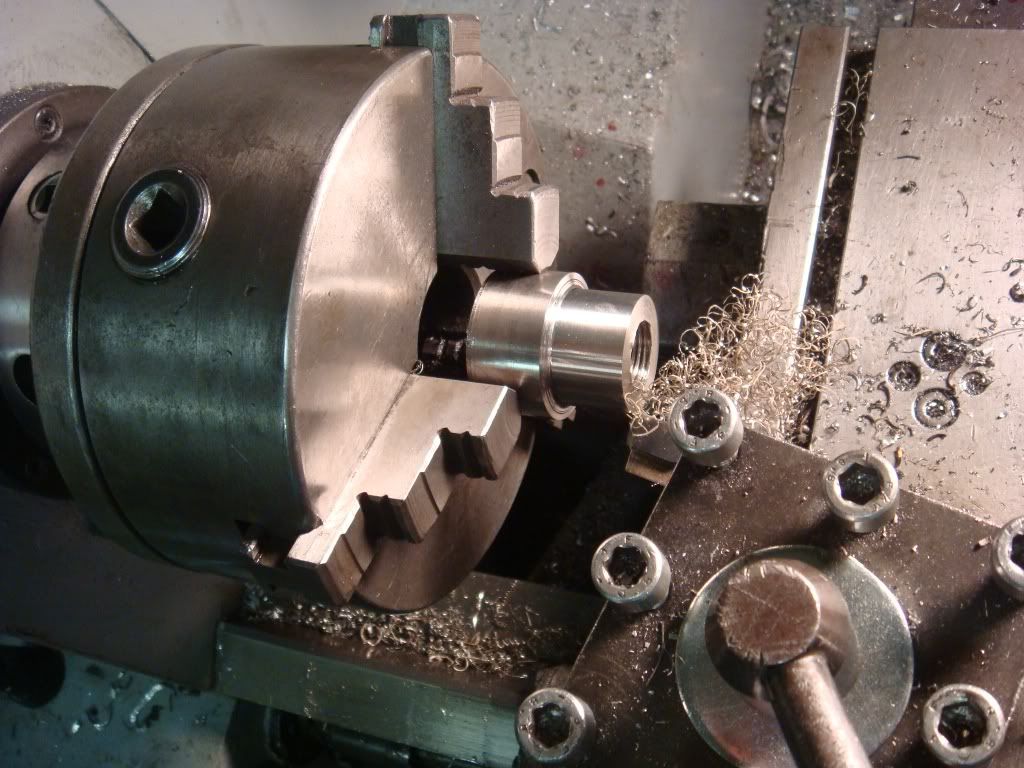
I really like this lathe. It is a beast. Yet is amazingly smooth. This is the near mirror finish I got using just a random ratty carbide tool and an indifferent speed selection:
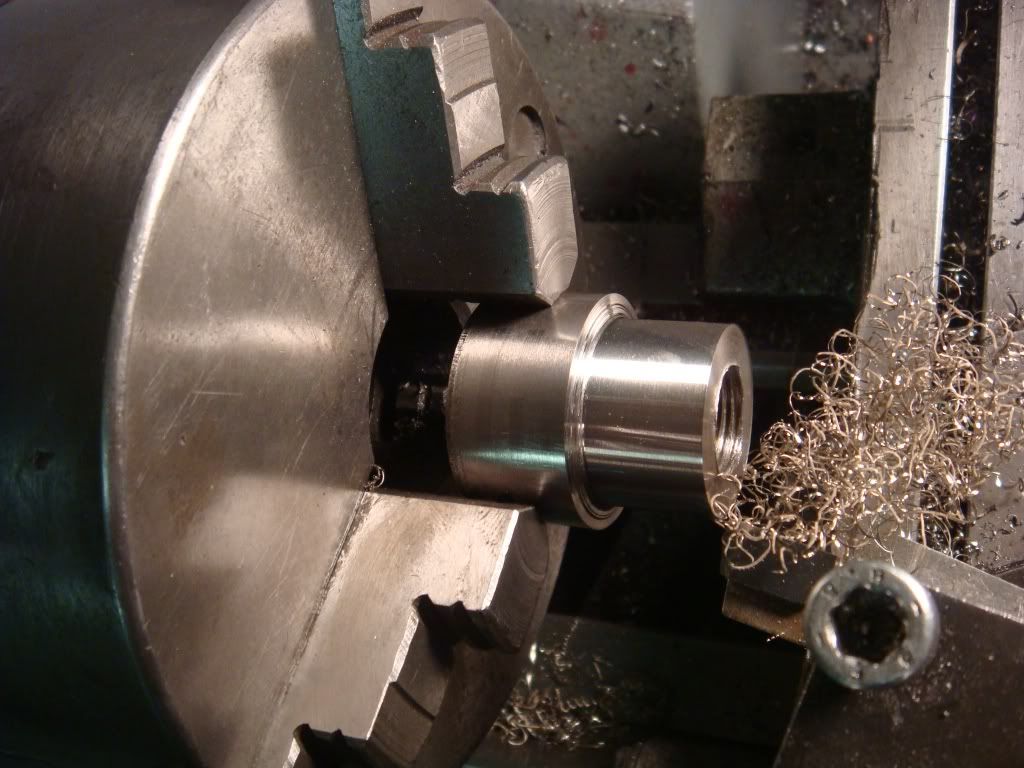
I used to hate cutting SS, but this damn machine eats it like aluminum. I think it cuts better than the best lathes I've ever used, including a hardinge HLV-H.
We then flip it around and cut the wider cirle that will hold it into the compund rest:
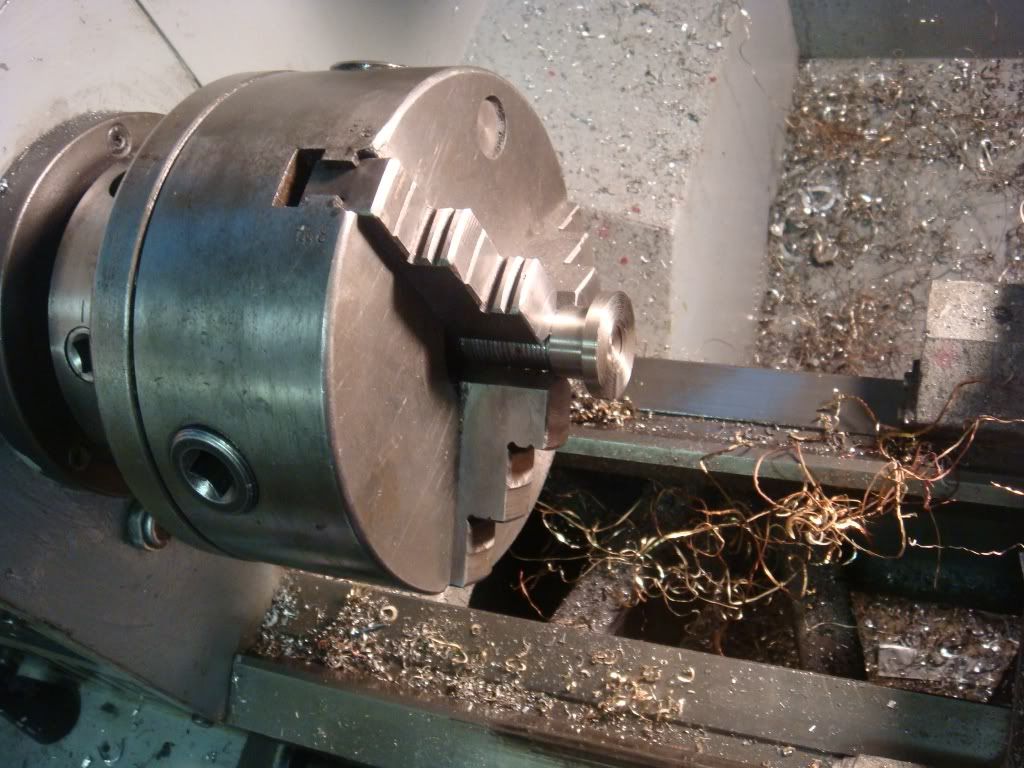
And we wind up wit:
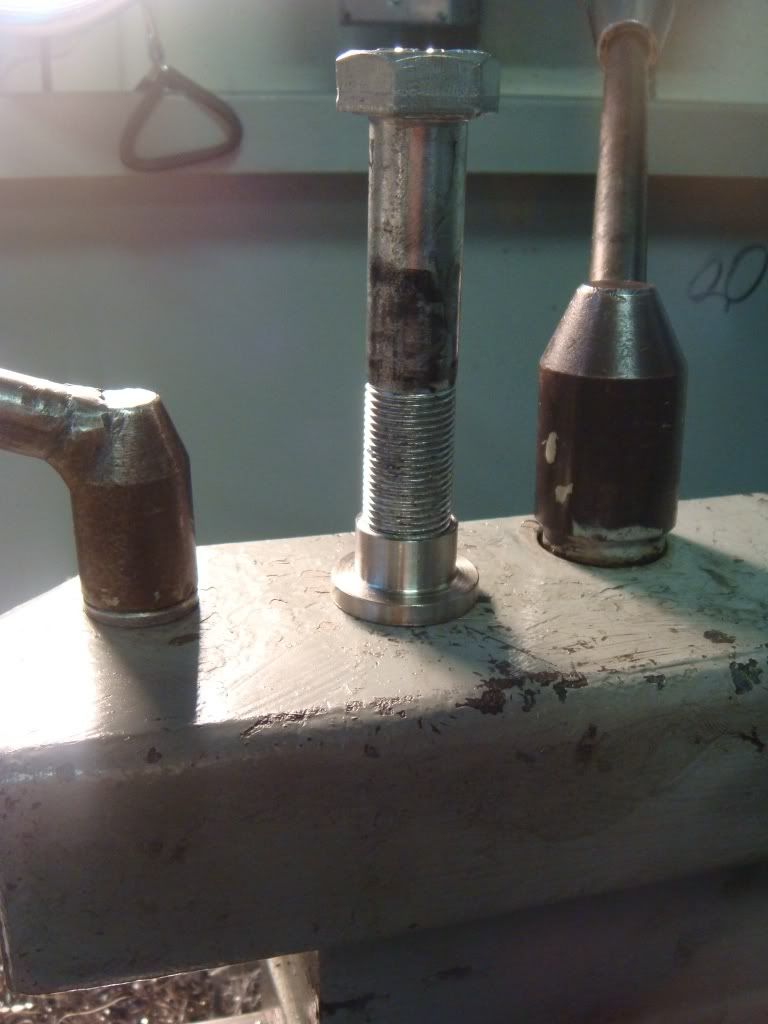
It's a bit small. I probably should have gone w/ a 1/2" bolt so that we'd have more material on the bushing. The plan is to try this out and see how it goes. Another mistake you can't see is that the base is a few .001s too big, so I really had to bang it in there. Once it comes back out I don't think it's going to be usable.
In any case, we now have a KDK where we need it!
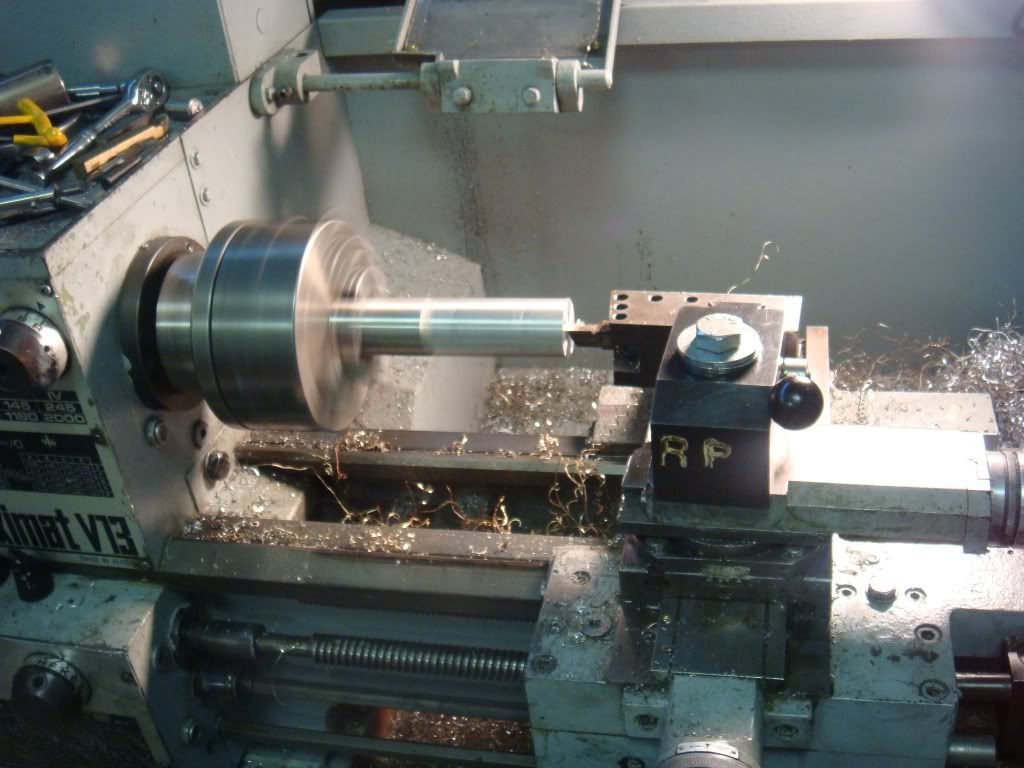
The post came with a hardinge lathe I have --- the initials on it are from the previous owner. It was sold after he died (like much of the equipment I own). Leaving them as a minor reminder to machinists that have passed seemed fitting.
No comments:
Post a Comment